Mendoza, Argentina
Gas distributors can now enjoy Galileo’s MX 1000 Pipeline Boosters
Galileo’s compression technologies keep improving the quality of life of Argentine households with two MX 1000 re-compression stations in El Pastal, Mendoza Province.
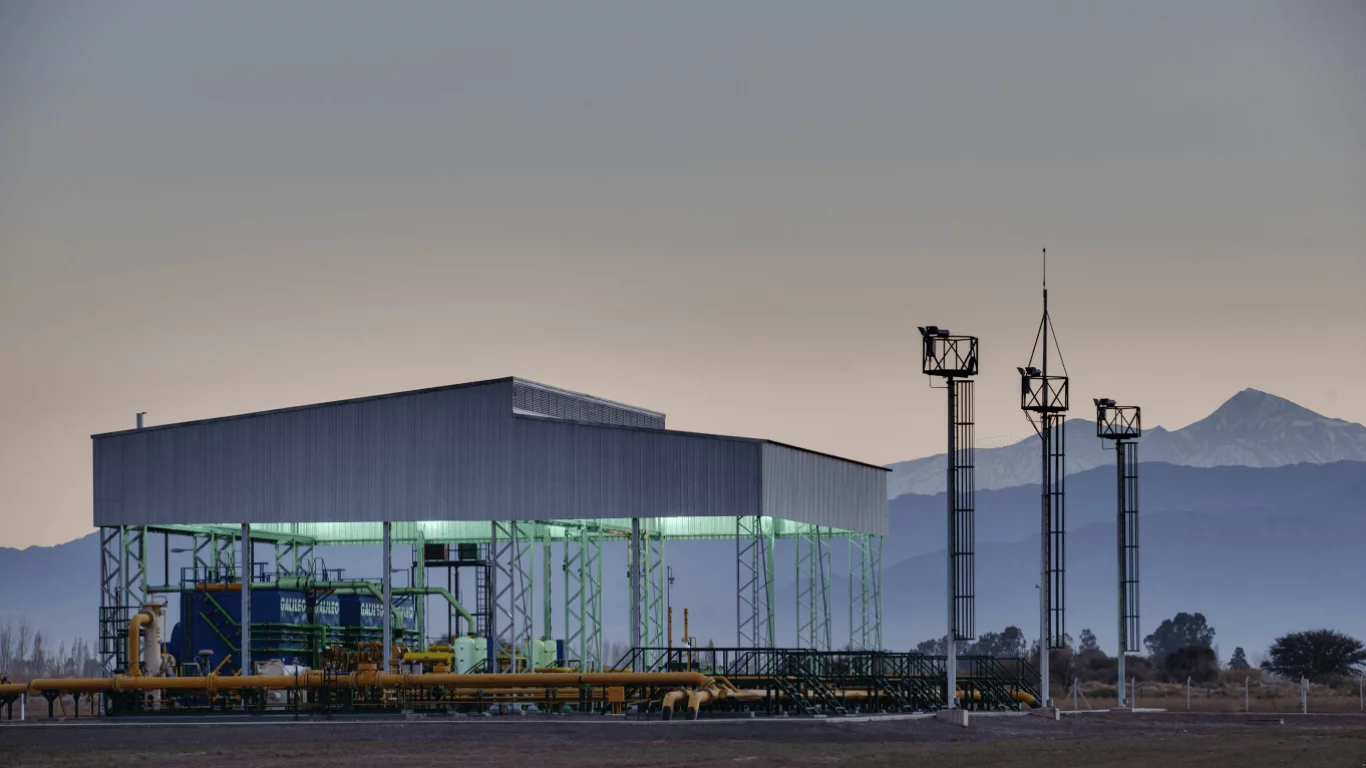
MX 1000 Pipeline Boosters at Boosting station in El Pastal, Mendoza Province, Argentina.
Experience, Design and In-house Manufacturing
Drawing on its thirty years’ expertise in the development of natural gas compression technologies, Galileo has relentlessly made remarkable progress in the manufacturing and design of equipments within the fields of Upstream, Midstream and Downstream for the Oil & Gas industry. In this process, Galileo has gone beyond packaging compression systems, to become the manufacturer of a wide range of compressors ranging between 30 kw (40 hp) and 1100 kw (1500 hp) power.
Galileo has its headquarters and manufacturing plant situated in the city of Buenos Aires, Argentina, and is currently the only company in Latin America with this technical capacity and specialization level.
These factors have given Galileo a natural and noteworthy response capacity to satisfy the main distribution companies and gas producers in Argentina regarding their Pipeline Boosters requirements in accordance with international standards. Galileo took this challenge and translated it into the development and manufacturing of its MX 1000 reciprocating compressors line.
A great experience close to the Andes: increased flow for households in San Juan, Argentina
Argentina is one of the countries with the biggest supply coverage in natural gas through distribution nets. However, this expansion is hindered by both severe pressure drops in pipelines and complications in homes & industries supply during the months of very low temperatures, when gas demand is five times higher than the average rate.
With temperatures below 0 °C (32 °F) between April and October, this situation was especially sensitive on the natural gas distribution net that reaches the Province of San Juan, upon which depend one hundred thousand customers, mostly homes.
To reverse this pressure drop situation, the gas distribution company Ecogas, built a boosting station in El Pastal, Province of Mendoza, with two Galileo Pipeline Boosters, both equipped with MX 1000 reciprocate compressors of 4 throws.
Each pipeline booster operates with an inlet pressure that ranges between 30 (435 psi) and 45 bar (653 psi), and an outlet pressure between 50 (725 psi) and 60 bar (870 psi). With this pressure regulation capacity, each unit provides a nominal flow of 1 million m3 (264 million gallons) per day.
While one of them operates nonstop, ensuring regular consumption in industries and homes, the other works as backup to flatten demand peaks and to meet future demand growh, which is estimated to rise by approximately 4% per year in the next five years.
To reverse this pressure drop situation, the gas distribution company Ecogas, built a boosting station in El Pastal, Province of Mendoza, with two Galileo Pipeline Boosters, both equipped with MX 1000 reciprocating compressors of 4 throws.
Design
Since this kind of equipments are subjected to high levels of demand, Galileo has developed its MX 1000 compressor packages pursuant to API 618 and API 11P standards, using specific CAD programs for its components design. Drawing on CAE/FEA programs, all critical components are optimized according to its dynamics and demand.
It is worth mentioning that these Pipeline Boosters have been conceived as modules so that the installed capacity can rise according to consumption demand.
In-house manufacturing
Quality focused, all manufacturing processes were performed pursuant to ISO9001 Standards and it is also worth stating that, except for the engine, the cylinder valves, and both command and safety valves, Galileo is the manufacturer of all packaged components, this being a worldwide distinctive feature.
Since Galileo is an in-house manufacturing company, both efficient operation and long service life for equipments are guaranteed. Moreover, this feature is complemented with a full standardization of primary components that can provide fast maintenance response.
MX 1000 Pipeline Boosters at Boosting station in El Pastal, Mendoza Province, Argentina
One of the components manufactured in-house is the MX 1000 compressors frame whose main body is made of stationed cast iron to ensure the absence of internal stress. The reciprocating four strokes compressors have a nominal power of 1100 kw at 1500 rpm. Each piston stroke is 110 mm (4.33 in) diameter and has a maximum imbalance of 0.90 kg (2 lbs) between strokes. As a result of these characteristics, compressors show really low levels of vibration during operation.
The crankshaft and connecting rod also follow the same criteria of reliability and long service life. These components are made of SAE 4140 forged hardening and tempering steel to ensure maximum strength in one single piece. These components are mounted on tri-metal bearings with forced feed lubrication with a 100 lts/min (26.417 gal/min) mechanically driven pump ensuring the required oil flow for each point of the compressor.
All body cylinders are made of nodular cast iron with large gas passages that have minimum pressure drop losses, air cooled and forced feed lubrication. They also have removable sliding fit liners that make field replacement work much more easily and faster in case of wear or any other eventuality. Cylinder liners, which are made of SAE 4140 like the 50.8 mm (2 in) diameter rods, are superficially treated with ion nitride to increase bore cylinders hardness and to reduce wear and corrosion. Piston rings, rider rings and wear bands are made of PEEK with carbon fiber and PTFE reinforcement, loaded with molybdenum disulfide to enhance wear resistance.
Galileo Field Services personnel monitoring performance of MX 1000 Pipeline Boosters at Boosting Station in El Pastal, Mendoza, Argentina.
All pressure vessels and piping stretching were manufactured and designed pursuant to ASME IX and ANSI 31b codes and, gas heat exchangers and engine cooling water pursuant to TEMA code. The two axial blade fans within each compressor skid make forced air circulate through heat exchangers. These fans take the necessary power directly from the engine crankshaft and through a robust Cardan drive and belts, with a simple and proven design that ensures smooth running, long life and easy maintenance.
Among third-party required components, Galileo has included a Caterpillar 3516 gas engine of 1340 hp in order to maximize the compression capability of its MX 1000 Pipeline Boosters. These 16V-cylinder engines take gas from the pipeline as fuel, ensuring fully operational equipment autonomy. Cylinder valves and rod packaging supplies have been entrusted to Hoerbiger, while secondary lubrication pump and distributor blocks with their control components have been supplied by Sloan Brothers Company.
Automatic operation and support
In order to ensure the requested/necessary flow levels, both units have automatic operation features, such as commanding starts and stops of the compressors based on the pressure of the pipeline or expected demand.
On the other hand,from Galileo’s headquarters located in Buenos Aires, the equipments’ operation is monitored in real time through Galileo SCADA System to guarantee quick technical support. Among operating parameters measured, are included:
- Compressor’s inlet and outlet gas pressure
- Suction and discharge gas temperature in each cylinder
- Suction and discharge gas pressure in each cylinder
- Each main bearing and each crosshead guide temperature
- Engine RPM
- Explosive atmosphere
Also, each frame stroke has a vibration control unit that records factors through SCADA such as:
- Loose or broken bolts
- Excessive clearance in connecting pins
- Loose or cracked rod nuts
- Liquid or debris in the cylinder
- Cracked connecting or piston rod
- Scoring in the cylinder
- Excessive crosshead/slipper clearance
- Other broken parts
- Additionally, a group of professionals and trained technicians provide field services complementing, this way, the monitoring Galileo Global Link - Scada System.
“Both our monitoring system and field support service are an essential part of our equipments’ development since we focus on long-term business relationships with our clients. This is why Galileo’s equipments are integrally designed. We offer design capabilities, industrial plant capacity and more than three decades of expertise in natural gas technologies. This has led us to tailor solutions for the Oil & Gas Industry, such as wellhead, gas-lift and gathering compressors; virtual pipelines; pipeline boosters; boosters for power generation, and special compressors for applications such as air or hydrogen (H2) compression”, says Osvaldo del Campo, Galileo CEO.